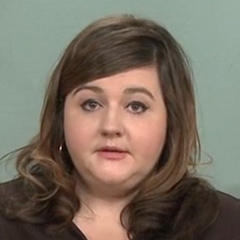
Types of Interfacing Fabric and Interfacing Sewing
Beth BradleyBeth Bradley teaches you about the various types of woven and nonwoven interfacing that can be fusible or non-fusible, and shows how to make the point of interfacing invisible. She also demonstrates how to cut the grain of the interfacing to match the fabric.
Interfacing is a really important part of any project, even though the whole point of it is to be invisible. And there's a huge range of interfacings, and it's really important to know about each kind so that you're selecting the right type of interfacing for the fabric that you're using and also for the part of the garment or the project, depending on the weight and the stability that you need in each area. So let's start by looking at woven interfacing, which is a very common type. And it's constructed just like fabric, just like any woven fabric, and so it has a lot of the same properties as a woven fabric. And it's available in both fusible and non-fusible, which is similar to other types of interfacing as well, but you can get either variety, depending on what you need for your project.
And it's important, before you use any interfacing, to preshrink the interfacing itself. A lot of the time if you experience puckering in your interfacing after you've washed a garment, it's because the interfacing wasn't shrunken first. So it's actually pulling away from the fabric after you've washed it. So before you start, before you start cutting a piece of any sort, preshrink the interfacing, and allow it to dry. So you can probably just leave it in cold water and then allow it to dry, and that should take most of the shrink away.
And preshrink your fabric as well, so they're both ready to go to be cut. And so with this woven interfacing, there's a lot of different weights and also a lot of different colors, depending on what color you need to match most with your fabric. So that's kind of the main thing to keep in mind when you're selecting interfacing, is that it matches the fabric as best as possible and gives you a few properties that you need, that the fabric might not have, depending on the application. So, for example, this is just kind of a very basic woven twill fabric. And it has some stability, but it's a little bit drapey.
So if you were making a skirt or a jacket out of it, there would be areas that you would need to add some firmness, like maybe near a buttonhole or a collar. And so this is an interfacing that has kind of a similar weight and won't take away too much of the nice texture and quality of the fabric, but it will add some stability to it. So here is the piece that I've actually fused the woven interfacing to, and you can see that now it has a lot more body to it than the original fabric. So this is a collar piece, like an undercollar. And that would give you a lot more crispness, and it will actually make the garment look a lot more professional and finished.
That's kind of the difference between something that looks homemade versus something that looks like you bought it, which is always the goal. So this, this is another type of woven interfacing that's fusible, and it's called a weft interfacing. It has an extra horizontal weft yarn that gives it a slight amount more stretch. You can see that the other woven interfacing that's just a plain woven interfacing does have a little bit of give, which works well with this fabric. So with either of these types, you're gonna just want to make sure to cut it on the same grain as the fabric.
So if your fabric is cut on the bias, you can cut woven interfacing on the bias as well, and that will just allow it to marry really well with the fabric and move the way the fabric needs to move. And you can use the weft interfacing also for knits because it's a little bit more delicate. So there are some knits that this would also be applicable for. The next type is the type that most people are most familiar with, which is the non-woven interfacing, which is also available in fusible and non-fusible varieties, depending on the type of fabric that you're using. And this, this type of interfacing is available in just a huge array of types and colors, so you definitely want to test it with your fabric to make sure that it's compatible.
So you can always just cut a swatch of maybe six inches of the interfacing and the fabric, and fuse them together before you start the project, just to make sure that the fusing works well and that it has the qualities that you want the end garment to have. So, for example, on one end of the spectrum, you have like a very, very lightweight, non-woven interfacing, and non-woven interfacing is constructed by bonding the fabric, bonding the fibers together, rather than actually weaving them on a loom. So you can cut this in any direction because it doesn't have a particular stretch in any particular direction, like the woven interfacing does. So this, you can cut in any shape that you need. So for this cotton lawn, I have this super light, very lightweight interfacing that's a fusible non-woven.
And in this case, you would want to choose an interfacing that still allows there to be some drape, like on a blouse or a dress that you'd be using this lightweight fabric for, but that you'd still need a little bit of rigidity, like in the placket or a collar, for example, but still allows for you to have that nice lightweight feel. So you can see that in this collar piece, when I fuse the interfacing, it actually gives it a nice rigidity that it didn't have before, where it was too, too soft and too flimsy. So on the other end of the spectrum, we have a really much stiffer non-woven fusible interfacing. So this is also in that same category but just much heavier and much more stiff. So this would be appropriate for maybe if you were making like a pocket flap for a jacket, and you just don't want it to have any curve, any flow.
You want it to stay nice and crisp all the time. So and also, this is in black. So you could use that for a darker fabric because you also don't want the interfacing to show too much through the fabric. So you could use a white for something like this. There's even varieties that are in like a flesh color or nude if you need that for a really sheer fabric.
Okay, so the next type is a knit tricot interfacing. And this is a fabric that's actually knitted, and then the fusible is applied to it. And so since it's a knit, it has inherent stretch in it that's way more stretchy than the woven interfacing or the non-woven interfacing. So this is really handy for when you're constructing a knit garment because it also has a lot of drape to it, like a knit. So, for example, this is a really, really drapey like rayon cotton jersey knit, and you can just see how drapey that is.
And this kind of has some of that same nice soft properties to it, and so you might be using this to construct maybe like a knit wrap dress or something of that nature. And even though you want that dress to be really, really flowy and drapey, there are some areas of it that still need some stability. So that's where this interfacing comes in really handy because you might need some stability along a neckline or if it has a collar. So this interfacing, since it has that inherent stretch, it actually moves along really nicely with the fabric. But you can see that compared to the un-interfaced fabric, it has a lot more rigidity, and it's nice and stable.
So it's a lot easier to sew also and be really precise. When you're making a collar or a cuff or something like that in the knit, then that's really helpful. And the knit tricot interfacing is actually lightweight and sheer enough that it's actually handy for like a chiffon or any kind of lightweight sheer fabric as well. If you needed to interface that, then this actually might be a better choice in some cases than a woven, even though chiffon is a woven fabric. And so if you're gonna try that, then just make a little test sample again, and fuse the interfacing to the fabric.
And then test it to see if you like the hand, and see if it's adhering well and gives the fabric the amount of stability that you need. So the next type of interfacing is a specialty interfacing that's just specifically for waistbands. Because waistbands are a part of the garment that you don't want to stretch or roll at all because it undergoes a lot of stress as you're sitting and standing. So you want it to be nice and crisp at all times and even more so than a collar or a cuff, which do need to be stiff, but this is really nice and rigid. So this interfacing comes, rather than coming on a bolt, it usually comes in a package of about three or four yards.
So you can use it for a few different garments. And it'll come with the finished width measurement indicated on the package. So you just want to make sure to match that with the pattern that you're using. So, for example, this kind that I have is one and a quarter inches wide. That's what it will finish at.
So, you will cut it according to your waistband measurement. And then this is how it looks as it comes out of the package. And it has a fusible and a non-fusible side. So you're going to place the fusible side down on your cut fabric piece. So you will press it onto the fabric from the fusible side.
And then when it's fused, it folds in half and just along that center perforated area, and then you have a really nice rigid waistband that looks very professional and like a ready-to-wear pair of pants. So the next type of interfacing is a horsehair canvas, which is a very stiff specialty interfacing that is mostly used for tailoring garments like a jacket or a coat. And it's far more rigid than just a regular woven interfacing. It actually has hairs woven into it, like a horsehairs tail is very coarse. So this, this gives a lot of coarseness.
And it's available in both fusible and non-fusible varieties, depending on the application that you need. And so, in this example, I'm using it on like an undercollar of a coat. And I have this wool herringbone, which you can see is pretty sturdy, but it does have some drape. And you don't want that drape in your collar or your cuff. You want it to be nice and rigid.
So this horsehair interfacing works really well for that. And now you can see how nice and coarse and rigid that piece is and will lay really nice and have very nice crisp edges on a corner. So the last type of interfacing that's a fusible is this stiff double-sided fusible interfacing. And it's the most rigid of all the types, and so you probably wouldn't use it for anything in a garment. But it's really, really excellent for accessories or craft projects because it has so much rigidity to it that you can give a nice stiff texture to just any kind of fabric, like a basic quilting cotton.
So you can use it maybe for like, the bottom of a purse is a good application or if you want to make a fabric vase or a fabric box. In this case, I've used it to make a mouse pad. And so you can see that it's slightly flexible but much stiffer and rigid than the garment-style interfacing. And I've just fused this quilting cotton to the front and then a felt to the back. And that works really well for that type of craft project.
And the next thing to talk about is non-fusible interfacing. And in most cases you can use a fusible interfacing because it saves you time, and you can just apply the interfacing to the fabric in one fell swoop as you're fusing. And it also makes it a nice even coating on the fabric. But in some cases, you can't use that because either the fabric is too sensitive to heat or it has properties that you don't want to disturb by applying a coating to the entire surface. So, for example, there's a non-fusible, a non-woven interfacing that's really stiff that I've used here, and I've used it, in this case, for like a flap for a pocket.
And you'd use it because you don't want to, I don't want to fuse the entire surface down, and I just want it to provide a nice underlining to keep that pocket nice and crisp. So, in this case, I've just kind of loosely basted it to the pattern piece. And after I've constructed the flap, then I can take away those basting stitches. I just did basting on the machine for that. So that's one way to do it.
If you have a more delicate fabric that requires a little bit more delicate touch, then you can use a plain, sheer organza fabric, which is a great underlining for a lighter weight or a drapier fabric. So, in this case, I have this linen blend that has a texture to it, and that's another good place to use a non-fusible because I don't want to disturb the texture of the fabric. You could use it for like a seersucker as well, where you don't want to get rid of those wrinkles because they're actually intentionally there, and you don't want to press them away onto the fusible surface. And so I've cut the organza shape just like I would the regular interfacing piece and leaving the seam allowance. And I'm gonna use a catch stitch, which is a hand-sewing couture stitch, and that is going to attach the interfacing to the pattern piece without fusing the entire piece at once.
And so that kind of allows them to move independently. Because this fabric has a lot of kind of drape and stretch to it that I don't want to remove from the fabric because I want it to still have that drapey look. So this will allow the two pieces to kind of shift independently of each other but still be attached. And so for a catch stitch, I'm just using this one single strand of thread, knotted at the end. And you're going to work the stitch from left to right.
So you can see I've already gone along the upper edge here. And I'm going to just take little bites out of the fabric so that they won't actually be visible on the face of the fabric, on the fabric right side, but it'll still be attached with this, just a tiny little bite of just a few threads. So I'll just take, I'm gonna just start along about a quarter inch from the organza edge and just take like a tiny loop, almost like making a little X with the thread and the needle. And then, as you can see, it just takes a couple threads from the front of the fabric, so it's barely visible on the face of the fabric. And you can imagine, too, if you're using a matching thread, it would be even less visible.
So it just takes that little tiny couple of threads. And then you come down about a quarter, an eighth or a quarter and a half of an inch outward from the last stitch, and do the same process, just making like a little X shape with your thread. And then you're just going to continue doing that along the entire edge of the piece. And that will provide a very secure, but also flexible stitch to keep those two pieces together. So the last thing to show you is how to properly fuse interfacing.
Because you might just think you can just iron it on, and it'll be all right. But if you take some extra time with it, then it actually will stay adhered much better, and it will be much more durable through washings and use. So I'm going to use a organza press cloth that is just a scrap of organza that you can use. And this will help the heat be applied more evenly over the fabric. And it also protects your iron in case you've accidentally put your iron on the, or put your interfacing with the fusible side up, which happens to everyone.
Then this will actually guard your iron soleplate from getting that sticky stuff melted onto it. So to start out with, I've already preshrunken my interfacing piece here. I'm using one of the weft woven interfacings in black because that will show the least under this black twill fabric that I have. And it actually has a really similar hand but will just give this a little extra stiffness as I'm sewing my collar. And I've trimmed away the seam allowances so that, I don't want to add extra bulk to the seam allowances.
I just want the extra body in the actual fabric of the piece. So I've centered that on the fabric piece. And the first thing to do is actually to just give it a little bit of a spritz. If you have a spray bottle, you can use that too. And that will just also allow the heat and moisture to distribute better.
And you can always check also on your bolt of fabric or your bolt of interfacing that you've purchased. A lot of the time, it will have specific instructions for the heat setting and for the amount of moisture that it needs to adhere. So always check that out too. But I've got this set on like a wool fabric setting. So it's not burning hot, but it has enough heat that it will melt the glue to the fabric.
So I've spritz that, and then I'm going to cover it with my press cloth. And I'm going to apply the pressure very evenly, and I'm going to work from the center outward. And I'm gonna use steam, again, to just distribute the heat and moisture really evenly. And you can leave it in one place for 10 or 15 seconds because that will allow a really firm grip. And so you don't want to be sliding it around because that might push the interfacing out of place.
So I'm just gonna slide it gently and just make sure that I've covered every single spot of the interfacing. For example, if you're making a tailored jacket and you're interfacing the entire front of the jacket, then you just want to make sure that you've interfaced every or you've adhered every single portion. So it's okay to go over the sections a couple of times. So I'm just making sure to get all of the corners without moving too much, using enough steam to distribute the heat. So you can take away your press cloth.
And the next most important thing to do is to not move it while it's cooling off. Because you might be tempted, as you're sewing, just to pull it right off the ironing board and bring it over to your sewing table and start stitching it. But if it's still warm, then the glue hasn't quite dried onto the fabric, and that can distort or it can detach and ruin that piece of fabric. So we're going to just allow this to cool off a little bit until it's cool to the touch. And then you can see that it's made a really nice, even, it's adhered really nice and evenly to the entire piece.
And it's not puckering or gapping on the other side. It's not causing those little ripples. And that piece is ready to be sewn to your jacket. So again, interfacing is just a really good way to make your projects look more professional. Even though it's invisible, it's very important.
And just pay attention, as you're selecting interfacing, to the type of fabric that you're using and also the placement of the interfacing.
What brand of Woven or Non-Woven interfacing should I use on Polyester Tshirts. I am making Tshirt quilts
Hi, which interfacing for a baby’s memory quilt would you use, I’m n the UK?
Do you pre wash fusible interfacing?
Very clear concise video. I have learned a lot. :)
Thank you, this was very helpful and informative!
Very comprehensive, thank you Beth.
thanks beth, a very informative video. although i have been sewing on and off for years, interfacing has been my nemesis. the facts and tips you shared have been very helpful.
Thank you for this informative and nicely presented article on interfacing and fusables, very helpful,with my current project of quilt piecing with men's neck ties where he need to @"support" the bias cut silk material.
Beth, this was a great demonstration of types of interfacing & when & how to use them! I know this is a very beginner question but after interfacing is pressed & adhered onto the fabric, when sewing it to the other piece of fabric, (right sides together), how far onto the interfacing do you stitch the pieces together before turning right sides out?
Excellent video, she did a great job with all the different types of interfacings and a very good explanation of how to iron on and stitch on. ( o :